Making IOT Work for the Customer
ManufaCTuring facilities Management
As a Maintenance Manager, ensuring equipment uptime is a key driver to purchasing a maintenance system. Ensuring equipment is available to Production when required directly impacts on the Business’ performance.
When Implementing a Maintenance system, the focus tends to be on a time based approach, at least initially. Most companies don’t make it to a Predictive Model. Preventative Maintenance assumes that by caring for a machine regularly there will be less performance issues.
A Predictive approach involves identifying leading indicators of machine downtime and then using sensor data to track this indicator. Using a threshold or tolerance value, sensor data can trigger an alert or work order in advance of machine failure.
The goal is to prevent equipment failure through knowledge and the intelligent use of data. The result is a significant improvement in uptime at a lower cost.
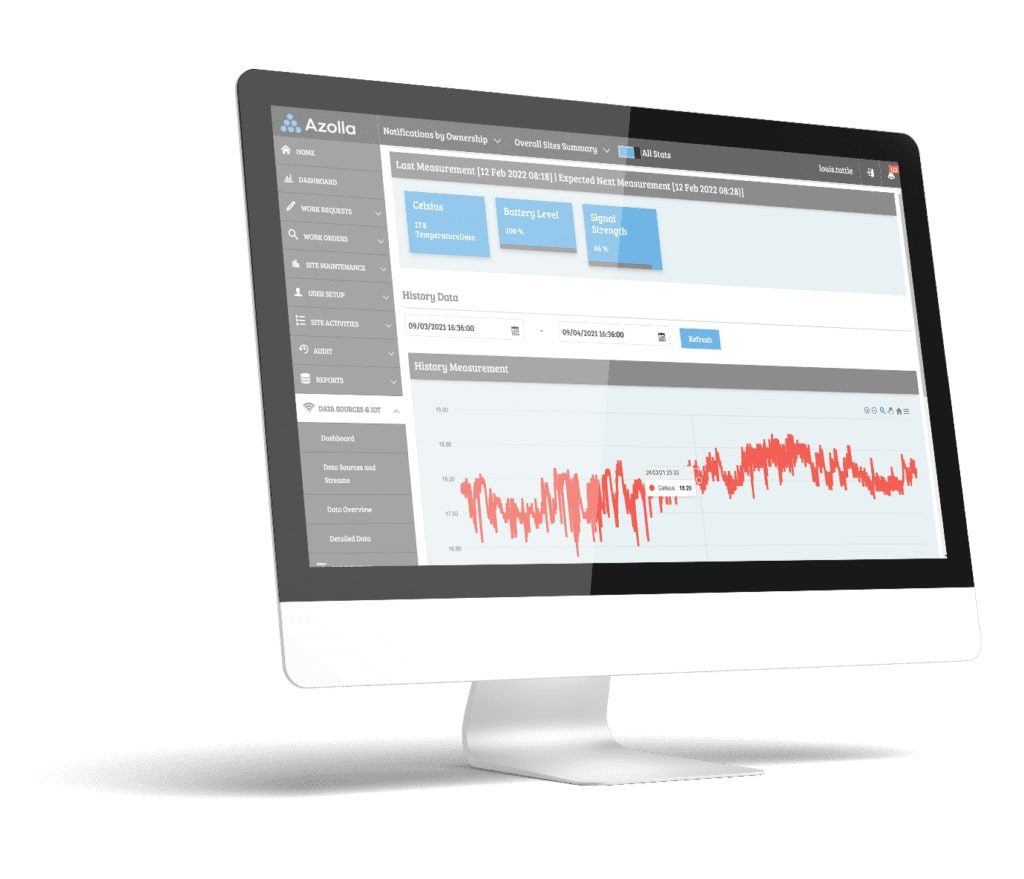
Why we are different
Azolla allows manufacturing companies to implement a predictive first approach to maintenance rather than defaulting to a time based approach. Using highly evolved sensor integration alongside the Azolla Rules Engine, sensor data from multiple sources can be interpreted and alerts or actions created to prevent asset failure. The Complex Rule Engine can allow multiple data points to be factored into the decision to create an alert or a work order based on a predefined tolerance value.
Based on Root Cause Analysis (RCA) or Failure Mode Effects Criticality Analysis (FMECA), leading indicators of failure can be identified and sensor data used to predict asset failure. As you evolve over time and as equipment ages, the Rules Engine can be altered allowing machine learning and human intelligence to create the optimum maintenance strategy.
Sensor data can be trended over time and reviews of asset failure during a RCA can be analysed to understand if new leading indicators are needed.
Azolla is designed to link to other systems including Building Management Systems (BMS), Supervisory Control and Data Acquisition (SCADA) or Enterprise Resource Planning (ERP) supporting Industry 4.0 initiatives. These data streams can be added to the Azolla model to improve asset performance monitoring but also to create a feedback loop or continuous improvement loop allowing an asset’s preventative maintenance plan to change over time.
What we do
We make implementing a Predictive Maintenance Model easy by using our Self Service IOT approach and allowing the End User to change the rules that interpret the sensor data themselves.
Scheduling & IOT
Azolla allows you to implement a Preventative Maintenance approach based on time but also makes use of machine sensor data to better inform when an asset needs maintenance.
Sensors can be linked to hard assets, monitoring performance and prompting early intervention if required. These sensors can also track equipment usage which can be used to efficiently maintain equipment and prevent over maintenance of assets.
IOT and AI
Data from Sensors can be trended over time and the Azolla rules engine that interprets the data can be changed by the end user as you learn. Data on usage or alarms can be linked to an event or email warning.Â
The Azolla rules engine allows for complex rules to be created so you can use more than one data point to make decisions about what’s the appropriate remedial action.
Paperless Maintenance
Using the Azolla App users can create work requests, complete work on the move including task lists or access data related to their equipment. Recommendations for follow-up action on PM’s can be suggested by the technician or contractor and these can be converted automatically to work requests.
The result is a truly paperless system that minimises the administration overhead of running a facilities management system but provides the data needed to make better decisions and ensure compliance.
Helpdesk
Allows Staff to raise requests through a PC or Phone, automatically routing high priority requests like cleaning to the correct team member. Â
Work assigned to external personnel can be distributed and acknowledged via email.Â
Health & Safety
Permits can be sent directly to the contractor with the acknowledgement and verification process occurring within email. Permits are linked to work orders, method statements can be attached and the administration approval process simplified.
Our Risk Assessment module allows risks to be identified, corrective actions to be issued and closed.
Supplier & Contractor Portal
A complete register of Contractors & Suppliers can be stored on Azolla along with their corresponding documentation including insurances. Renewal notifications can be sent directly to the contractor for documentation due to expire while Suppliers can then log onto the Supplier portal to upload their documentation for review.
Customer Success Management
We learn by doing and listening to the Customer
User Population
Sites mobilised for clients
Assets Added
Active Sensor Data Points
Return on Investment
The Key to implementing a maintenance system is to understand the problem you are trying to fix.Â
Up to 80% of Equipment Maintenance can be inefficient because over time tasks lists for weekly, monthly and yearly checks tend to overlap.Â
Root Cause Analysis of breakdowns tends to also lead to increased checks on equipment to prevent their reoccurrence without understanding the likelihood of the initial failure. The check remains in place out of habit rather than need.Â
Azolla uses Artificial Technology (AI) to help make better decisions. Using the complex rule engine, data gathered from equipment is interpreted in an evolving way with new alerts raised or old events stopped depending on the experience with the equipment. The system learns from you and the data and the result is a more efficient approach to protecting your equipment.Â
- Reduce Unnecessary Maintenance up to – 80%
- Reduced Equipment Downtime -50%
- Improved Repair Times (MTTR)
- Be Compliant and Audit Ready- 100%