Making IOT Work for the Customer
Office Facilities
Management
The days of a Facility Manager are rarely boring. People’s expectations are high and there is a lot of complexity.
From ensuring that important statutory checks happen on time, managing contractor visits to the site including issuing Permit to Work, to dealing with helpdesk requests. Everyone expects an immediate response while hybrid working adds new complexity.
The Azolla IOT Sensor packs help support the Return to Work initiative using Occupancy Management sensors which can then allow you to implement On Demand Cleaning & Hot Desking. CO2 monitoring allows you to help reduce the sources of infection while paper and towel sensors in toilet areas help to promote hygiene levels.
What we do for corporate and office fm
Azolla was built by Facilities Managers for Facilities Managers. Technology serves best when it is understood by those creating it.
Help Desk
- Real-time Issue Tracking: IoT sensors and devices can provide instant data on facility issues, enabling quicker response and resolution times.
- Predictive Maintenance: IoT data can help identify potential problems before they escalate, reducing downtime and enhancing user satisfaction.
- Automation of Service Requests: IoT solutions can streamline the process of reporting issues and requesting help, improving efficiency.
- Performance Metrics: IoT analytics can measure the performance of help desk services, facilitating continuous improvement.
Scheduling of Statutory or Non Statutory Work
- Optimised Workflows: Help automate scheduling and resource allocation, ensuring efficient use of personnel and assets.
- Compliance Tracking: Aiding in monitoring and documenting compliance with statutory requirements, reducing the risk of penalties.
- Resource Utilisation: Providing insights into equipment and space utilisation, helping optimize scheduling.
- Data-Driven Decision-Making: Inform better scheduling decisions based on historical data and real-time conditions.
Supplier & Contractor Management
- Performance Tracking: Monitoring supplier or contractor performance in real-time, ensuring service level agreements (SLAs) are met.
- Automated Permit Issuance: Streamline the process of issuing permits, reducing administrative overhead and errors.
- Cost Optimisation: Data-driven technology can help identify cost-saving opportunities and negotiate better contracts.
- Transparency: Technology solutions provide transparency into supplier and contractor activities, reducing disputes and improving accountability.
Permit to Work
- Access Control: Advanced technology can control access to high-risk areas based on permit status, enhancing safety.
- Real-time Monitoring: Cutting-edge sensors can monitor activities covered by permits, ensuring compliance with safety and environmental regulations.
- Audit Trail: Technology solutions can create a detailed digital record of permit activities, aiding in compliance reporting.
- Automated Permit Issuance: Technology can streamline the process of issuing permits, reducing administrative overhead and errors.
Occupational Management
- Workspace Optimisation: Reducing real estate costs while ensuring a productive work environment.
- Occupant Safety: Can track and manage safety protocols and occupancy limits, ensuring a safe working environment.
- Resource Management: Streamlining the allocation of resources, such as meeting rooms and equipment, to improve overall operational efficiency.
- Employee Satisfaction: Effective occupational management leads to improved workplace conditions, promoting employee well-being and satisfaction.
Cost and Budget Control
- Expense Tracking: Financial software can monitor and categorize facility-related expenses, providing visibility into the financial health of the facilities management budget.
- Budget Planning: Technology assists in creating and managing budgets for facilities maintenance and upgrades, helping control costs.
- Cost Reduction: Data-driven insights identify opportunities to reduce operational expenses, optimising FM costs.
- Strategic Planning: For long-term financial planning and capital investment strategies, enhancing cost control.
Auto Allocation of work
- Resource Efficiency: Automated allocation of work orders and tasks optimises the deployment of maintenance and repair teams, reducing downtime.
- Workload Balance: Technology ensures an equitable distribution of work, preventing overburdening of facility management staff.
- Time Savings: Automated allocation minimises administrative overhead, allowing staff to focus on critical tasks and improving response times.
- Service Quality: Efficient work allocation enhances the quality and speed of service provided to maintain facilities.
SLA Management
- Service Quality Assurance: Technology tracks and enforces service level agreements (SLAs) in facility management, enhancing tenant and client satisfaction.
- Performance Metrics: Provides insights into service performance, allowing continuous improvement in facility management services.
- Dispute Resolution: A clear record of service commitments, aiding in conflict resolution and contract compliance.
- Accountability: Technology ensures service providers are accountable for meeting SLAs, fostering transparency and trust in facility management.
NFC / QR Code Tagging – ensuring work is closed
- Work Order Verification: Verifies the completion of maintenance tasks and work orders, ensuring quality control.
- Accurate Records: Provides reliable digital records of work closure, simplifying auditing and compliance in facility management.
- Error Prevention: Reducing the risk of manual errors in documentation, enhancing the quality of records.
- Operational Efficiency: Streamlines the work closure process, reducing paperwork and ensuring that nothing falls through the cracks.
Critical infrastructure monitoring
- Asset Protection: Safeguards critical facility infrastructure by providing real-time threat detection and proactive response.
- Preventive Maintenance: Offer early warnings for maintenance needs, reducing the risk of costly downtime in critical facility systems.
- Data Integrity: Critical infrastructure monitoring ensures data center reliability, minimising the risk of data loss or system failures.
- Regulatory Compliance: Helps facility management adhere to industry regulations and standards, mitigating compliance risks.
Configurable Dashboard Reporting
- Data Insights: Configurable dashboard reporting offers real-time visibility into key facility management metrics and performance indicators.
- Decision Support: Dashboards empower facility managers to make informed decisions and quickly respond to issues or opportunities.
- User-Friendly Interface: Easy to navigate, making data analysis more accessible for facility management staff.
- Continuous Improvement: Real-time dashboard reporting supports performance monitoring and ongoing optimization of facility management services and resources.
“Through the use of Azolla, we had an 18% ROI for On-demand cleaning in a new 430,000 sq Ft
client location”
CORPORATE AND OFFICE FM USE CASES
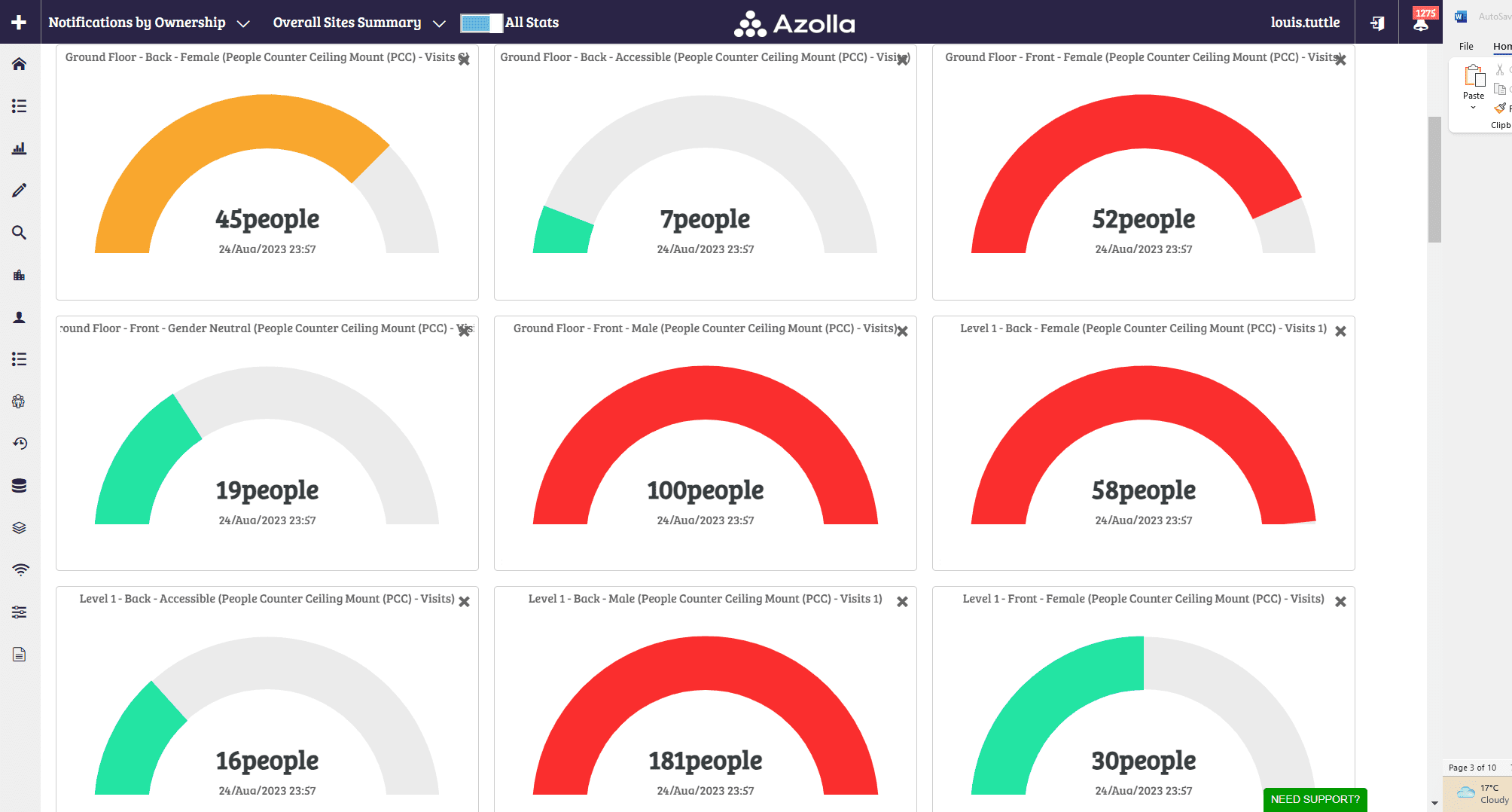
Occupancy Management
Optimise space utilisation, reduce costs, and ensure health and safety compliance with occupancy management software. Enhance the workplace experience for employees by providing efficient space allocation and usage.

Escalation Management
Swiftly resolve customer issues, boost satisfaction, and gain data-driven insights with escalation management software. It streamlines issue resolution, reduces workload, and enhances customer retention.

On-demand Cleaning
Efficiently allocate cleaning resources, maintain cleanliness, and improve customer satisfaction with on-demand cleaning software. Real-time monitoring and response ensure clean and safe environments.
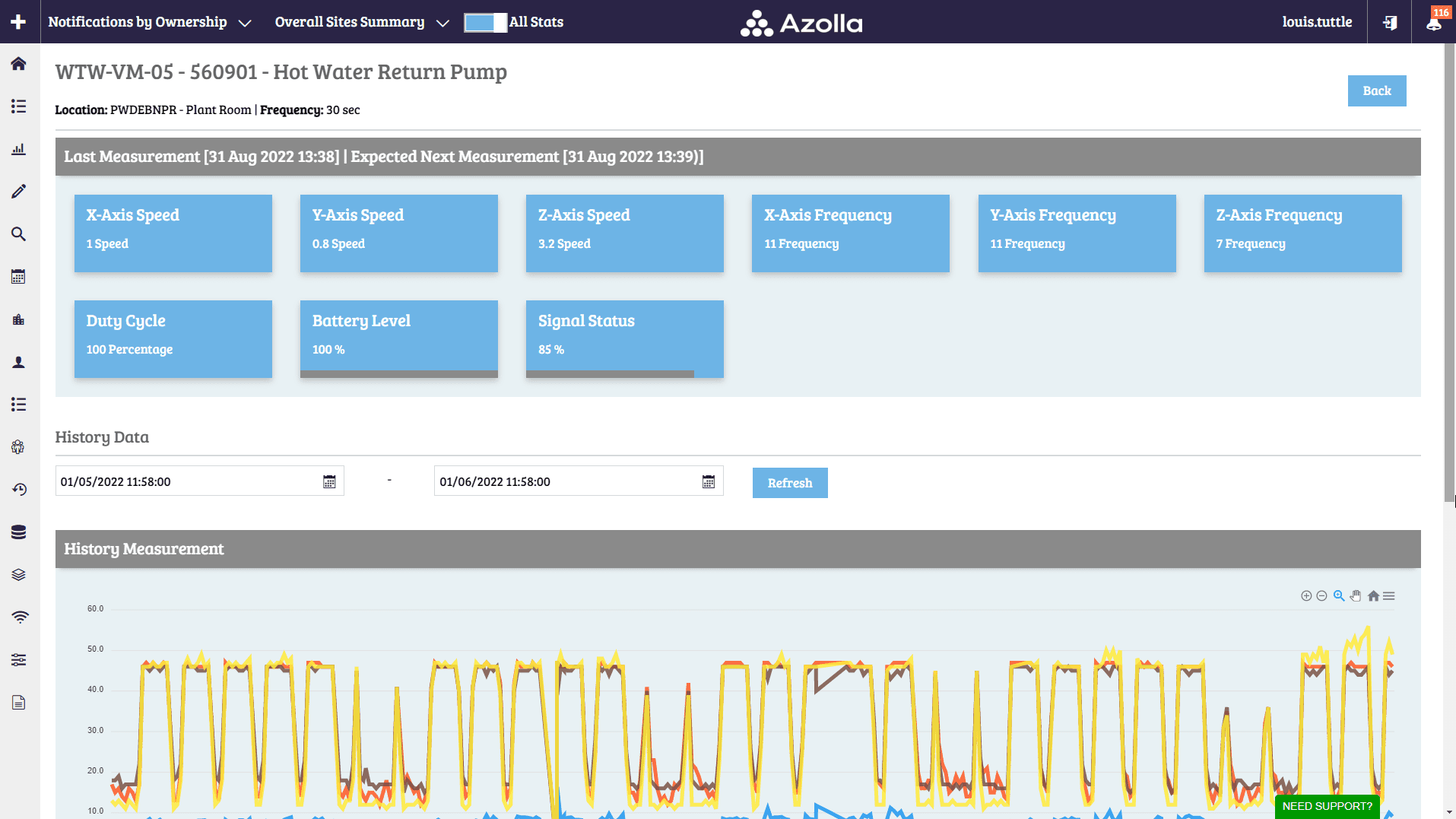
Asset Management
Optimise asset utilisation, save costs, ensure compliance, and implement predictive maintenance with asset management software. Enhance equipment performance and extend asset lifespans while maintaining accountability.
Corporate and Office FM REturn on Investment
It is possible to lower costs by adopting best practice.
Moving to an On Demand cleaning model lowers costs by targeting resources where the need is most.
Occupancy Management allows you to plan resources around building usage as well as lower energy and catering costs.
A Planned Maintenance job is 3-5 Times More Expensive than an Unplanned Job. Costs are lowered by lower overtime and contractor call out charges.
Using sensor technology to monitor equipment in real time lowers callout charges while allowing for earlier resolution of issues.
- On Demand Cleaning Model Lower Cleaning Costs by- 20%
- Occupancy Management helps to lower Catering Costs -12%
- Planned Maintenance Model lowers Overtime and Contractor Costs – 20%
- Sensor Monitoring Lowers Call out charges by – 8%
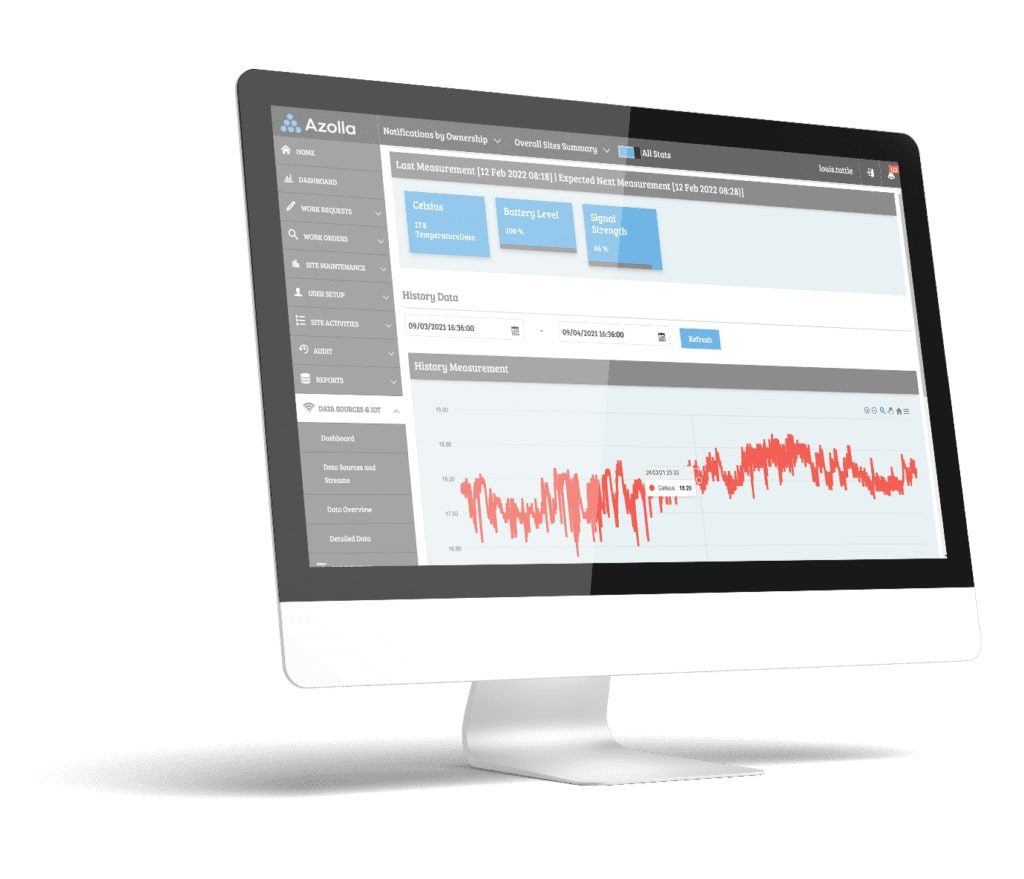
Why we are different
Azolla was built by Facilities Managers for Facilities Managers incorporating key functionality used to schedule both planned and reactive work, track contractor entry, adherence to Service Level Agreements (SLA) and report on all completed work.
Azolla is designed to allow you to implement IOT sensor technology from the start. From tracking temperatures in a server room or leak detection in an office, Azolla allows you to track your building in real-time. Reactive work can also be routed to third-party contractors via email and responded to electronically, all in one place. This creates a full asset history, tracks the total cost of ownership and facilitates real-time reporting.
Concepts like Smart buildings become practical. With the Return to Work drive, this technology can be used to track occupancy levels allowing you to prioritise On Demand cleaning in areas where they are needed and not just on schedule. Soap, paper and towel sensors can monitor remote toilet and shower areas and schedule replenishment based on need.
Asset failure can be monitored with leading detectors like power, temperature or vibration sensors. Each sensor can be linked to a different workflow, alerting the correct resource automatically, especially during ‘out of hours’. If this data sits within a Building Management System (BMS), then it can be integrated in, resolved and reported on in one system.