Why Permit to Work Systems Are Critical for Facilities Management
In the complex environment of facilities management, safety and compliance are essential. A critical tool to ensure a safe working environment is the Permit to Work (PTW) system. Azolla’s CAFM (Computer-Aided Facility Management) software includes a sophisticated electronic Permit to Work module that simplifies the management, approval, and monitoring of permits, ensuring that facilities operate safely and efficiently. In this blog post, we’ll explore how Azolla’s PTW system works, the benefits it offers, and why it’s so important for facilities management.
Understanding the Azolla Permit to Work Module:
The Azolla PTW module is designed to streamline the entire permit process for both internal teams and external contractors. Whether it’s routine maintenance or more complex tasks, this tool allows facilities managers to issue permits, monitor progress, and ensure compliance, all from one unified platform. Here’s a step-by-step breakdown of how the Azolla PTW system works:
Accessing the Permit Module:
To begin, users navigate to the “Health and Safety” section within Azolla, followed by selecting “Permit to Work.” From here, they can create a new permit by choosing the contractor or supplier responsible for the task, including the specific contact person overseeing the work.
Creating a Permit:
Users enter a detailed description of the work to be undertaken and specify when the work is scheduled to take place. They can also notify internal teams by selecting relevant members who will be automatically updated via email when the permit is approved, cancelled, or closed. If identification or Risk Assessments and Method Statements (RAMS) are required from the contractor, this can be requested within the system.
Identifying Hazards and PPE:
One of the most important stages of the permit process is identifying potential hazards. Users can select relevant risks associated with the task and specify the Personal Protective Equipment (PPE) required to mitigate these risks, ensuring all workers are adequately protected.
Linking Work Orders:
Permits can either be linked to specific work orders or issued as standalone documents. Once the permit is complete, it can be sent directly to the contractor, who will receive an email with a link to access and review the permit.
Contractor Review and Approval:
Contractors can edit certain details of the permit, confirm the work conditions, and select the person who will be attending the site. If RAMS are requested then the Contractor can attach at this stage for review. They are also required to acknowledge the work conditions and hazards likely to be present. If any mandatory questions have not been answered, the system will prompt the contractor to complete them.
Permit Authorisation:
The Permit Authoriser within the organisation can review all open permits, check the attached RAMS, and assess the contractor’s responses. After this review, the authoriser can approve or decline the permit, providing the contractor with a reason. Once approved, Azolla automatically generates a PDF of the permit and sends it to the contractor. Using our email notifications any internal team impacted by the Permit is automatically updated if the Permit status changes.
Closing the Permit:
Once the contractor arrives on-site and completes the work, the permit can be closed electronically. Should the work need to be suspended or rescheduled, the permit can be reissued at a later date. All previous permits are stored within the system, allowing for easy access to historical data and related documentation for future audits or reviews.
A Realisation in the Meeting Room: The Missing Piece in Their Operations:
During a recent meeting with a potential client, a large facilities services company, we were walking them through the various features of the Azolla CAFM system. As we reached the Permit to Work module, their Operations Manager, Sarah, perked up with clear interest. She had been quiet for most of the meeting but suddenly interrupted, saying, “This is exactly what we’ve been struggling with!”
Sarah went on to explain that their current method of managing work permits was outdated and largely paper-based. They were relying on physical forms, which were often delayed or lost in the shuffle between teams. Contractors would sometimes show up on-site without proper documentation, causing delays and, more importantly, increasing safety risks. She added that their current process had no efficient way of tracking who was informed or ensuring that everyone involved had seen and approved the permits before work commenced.
When we demonstrated how easy it is to create a permit in the Azolla system—selecting the contractor, specifying work details, identifying hazards, and notifying internal teams—Sarah immediately saw how much time and effort this system could save. The automated notifications, the ability to attach Risk Assessments and Method Statements (RAMS), and the clear tracking of approvals within the system struck a chord with her. She even noted, “We’ve had incidents where contractors arrived without understanding the work conditions, and if we had a system like this, it could have been avoided.”
After we finished the demo, Sarah shared that they had been exploring solutions to streamline their permit process for months but hadn’t found anything that clicked—until now. She was especially impressed with how the system integrates work orders with permits and how all relevant documents are stored in one place for easy access. The ability to reissue or suspend permits without starting the entire process from scratch was also a huge plus for them, as their projects often faced unexpected delays.
In the end, Sarah’s team acknowledged that Azolla’s Permit to Work module was the missing piece in their facilities management toolkit, and it quickly became a focal point of our ongoing discussions. They realised that not only would it improve their compliance and safety standards, but it would also drastically reduce administrative burden and miscommunication between teams and contractors.
It was clear that the Azolla PTW system was exactly what they needed to bring their operations into the digital age and ensure a safer, more efficient working environment.
The Benefits of Using Azolla’s Permit to Work System:
The Azolla PTW system provides significant advantages for facilities management, going beyond just compliance. Here are some of the key benefits of having such a system in place, backed by measurable improvements:
Increased Compliance:
Implementing a digital PTW system like Azolla can improve compliance with health and safety regulations by as much as 40-50%. The automated checks and mandatory fields ensure that all necessary precautions are taken before work begins.
Reduction in Administrative Time:
Transitioning from a paper-based to a digital permit system can reduce the time spent on administrative tasks by 30-40%. This includes filling out forms, chasing approvals, and managing documentation, freeing up staff to focus on higher-value tasks.
Fewer Incidents or Safety Violations:
Organisations that use a formalised PTW system typically see a reduction in safety incidents or violations by up to 25-30%. The ability to identify hazards and specify controls in advance helps prevent accidents on-site.
Improved Contractor Onboarding Time:
With automated notifications and centralised documentation, contractor onboarding times can be reduced by 20-30%, ensuring that all necessary approvals and information are provided without delays.
Enhanced Communication Efficiency:
The real-time notifications and updates within the system can improve communication between internal teams and contractors by up to 50%, reducing miscommunication and ensuring that everyone is informed about permit status changes immediately.
Audit and Inspection Readiness:
Organisations using a digital PTW system often report that their readiness for audits and inspections improves by 30-40%, as all historical permits, RAMS, and safety documentation are stored centrally and are easily accessible for review.
Closing Thoughts:
Azolla’s Permit to Work module is an invaluable tool for modern facilities management, playing a crucial role in ensuring that all maintenance, operational activities, and contracted work are carried out safely and in full compliance with regulations. The integration and approval within Microsoft Outlook simplify the process and improve the adoption levels of this approach helping improve compliance levels. By simplifying the permit process, improving communication, and ensuring that safety is prioritised, Azolla contributes to creating a safer, more efficient, and compliant working environment.
Incorporating a robust PTW system not only protects your workforce but also streamlines operations, enhances accountability, and ensures that all activities are managed effectively. For any facilities management team looking to improve safety protocols and operational efficiency, Azolla’s PTW system offers a powerful solution.
We have a demo video of our Permit to Work, if you would like to view this contact us and we can send it to you or if you would prefer a live demo where you can ask questions, get in touch!
Get in touch below if you would like to find out more about Azolla for your organisation or client sites.
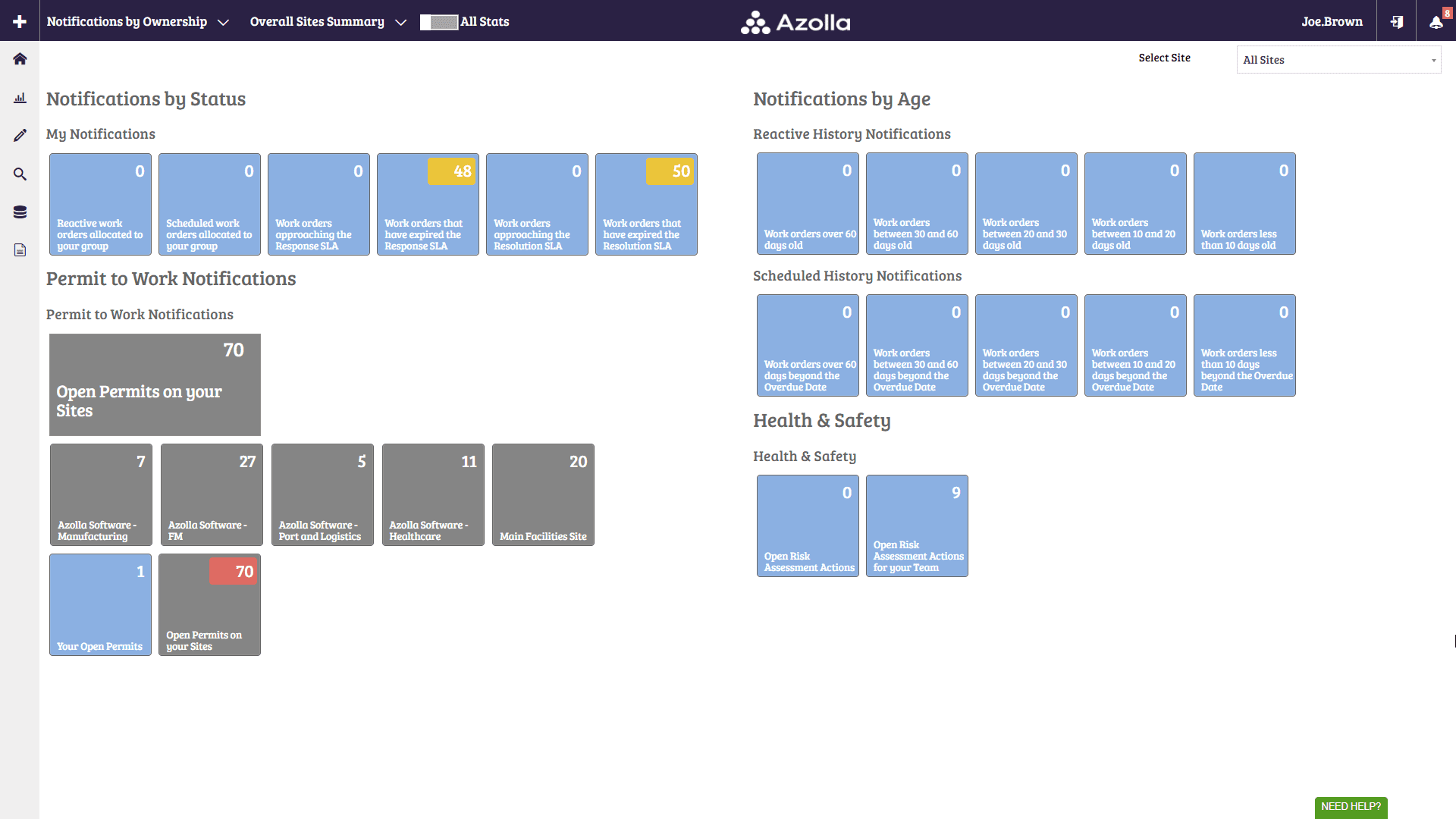